I'm the proud new owner of a
microCarve A4 CNC machine. I'm still getting it built up--I got my motors and motor driver three days ago and the A4 just arrived yesterday.
Yesterday and today I was working on an enclosure for my Gecko G540 driver and the power supply for it and the motors. After looking around at what I had on hand, I decided to "repurpose" an old UPS's enclosure:

The Enclosure, after the guts were removed.

The original back plate.

And the Inside
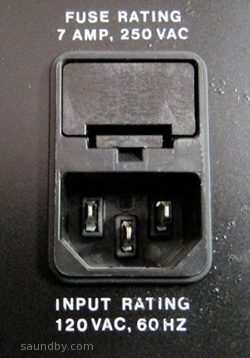
A Fused Mains Plug--Very Handy!

Here's where the Gecko will fit, more or less.
My original plan was just to use a nibbler, starting at the hole for the phone jack for the UPS. I scribed my cut lines, then started cutting with the nibbler. About an inch into the work, the nibbler broke. Did I mention that I'd modified this nibbler in the past to cut plastic? I made it so that its jaw would open wider. This weakened the nibbler a bit, but hey, who needs strength for cutting plastic?
Then I went and cut some metal with it. It wasn't up to that job any more.
I spent much of the day yesterday trying to buy a new nibbler. I went to five different places nearby. Four of those places had never heard of a nibbler, at least three seemed to think I was making it up. The last had heard of nibblers, but they didn't have any.
So I came back home and got to work with other tools. I finished the job about noon today. It was a lot more work, but the results are decent, even if they're not quite as clean as I can get with a nibbler. Plus it made a lot of steel filings. Dremel, cutoff wheels, cold chisel, files, grinding stone and hammer were among the tools used.

The Gecko, in its new home.

The Gecko from the back.
Since I had to take care of all those filings, I did a pretty thorough cleaning of my bench so that I'd have a place to assemble the A4 without any further delays. My next image reveals wood which seldom sees the light of day:

The top of my bench. Stains are just Tapmatic fluid that hasn't dried yet.
It looks like it's outside because of the window. In fact, it's in a second garage that was added outside the house's original garage. The original garage's windows were just left in place when the prior owners added the second garage.