- It was in the open air. Sawdust and plastic chips were flying everywhere.
- I wanted my workbench back for other projects!
So it was time to take time off from making cool CNC projects and time to make an enclosure. I spent quite a bit of time thinking through what I wanted. If I put the computer and CNC side by side, it'd take up too much room in the shop. I tried a test arrangement of putting the computer below the CNC, the display above the CNC, and the keyboard and mouse in a drawer just under the tabletop that the CNC sat on. This did my neck no favors at all.
Finally I settled on putting the CNC itself a bit higher, with the computer completely underneath it. This worked out, barely. I had to replace my old CRT monitor with a lower-profile LCD display to get the heights I wanted. It was worth it.
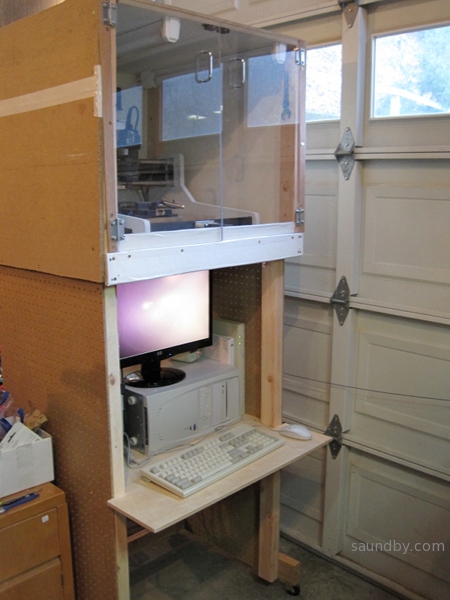
The desktop is at 26 inches above the floor, the bottom of the CNC is at 48 inches above floor level. It's low enough to handle the tools, parts, and everything else inside as well as keep an eye on the machining as it goes, though an optimum height would probably be a bit lower. A different arrangement of the computer stuff down below could probably allow someone else to make theirs about six inches shorter, if they don't mind looking down at their computer monitor rather than propping it up on the computer cabinet for a comfortable height, as I did.
The desktop holds the computer, monitor, power control center, CNC power supply and Gecko G540 control unit, wireless network hub, keyboard, mouse, and an occasional can of soda (with care).

The CNC box has removable panels on the back and sides. The back panel is in three sections, so that a middle section can be taken out for working with stock that's too long for the enclosure. This leaves a panel at the bottom to catch chips, and a top panel to trap some of the high-flying chips. If necessary, one or both of the front doors can be left open with longer pieces, a bottom panel will still cover the lower three inches of the front to trap some of the chips from spilling out. I thought about making sectioned doors, but this project was already getting too complicated.

The top box can lift off of the base with the computer desk. It has small feet that rest inside the uprights on the base and lock it in, as well as a pair of angle brackets that screw into it. Basically the power and control cables that run into the box through the two PVC feed-throughs are are disconnected, the box is lifted off the top of the base (a two-person operation when the CNC is in there!), then set on its feet where ever it suits you.
The base has casters on the bottom, so I can roll it around the shop or out onto the concrete apron outside if I feel like doing my CNC work under the sky. ;)
I plan on adding a vacuum motor and dust trap below the desktop when the urge to take things a step further strikes. I'll cut another feed-through into the box for the vacuum as well as an air intake for the enclosure. Until then I'll just be reaching in with the hose of a nearby canister vacuum to clean things out.
Nice enclosure. Out of interest, how much does it reduce the noise by?
ReplyDeleteI live in a unit and I'm looking at buying a Microcarve machine (specifically John's BBOX); however as there are a number of neighbours in relatively close quarters, noise is a bit of an issue. I was thinking if I do get a CNC machine an enclosure would probably be necessary and could even be lined with foam.
It reduces the noise a LOT. The noisiest place is in front of the acrylic doors. Part of the reason I needed to build this is that my wife is working on the other side of the wall during the same times that I like to go out in the shop and work.
ReplyDeleteThis makes it inaudible to her.
Plus, I don't need to wear hearing protection. I still wear eye protection when I'm watching through the doors. I don't have complete confidence in the ability of plain acrylic to stop a flying bit. I may upgrade the doors to Lexan this winter, though.